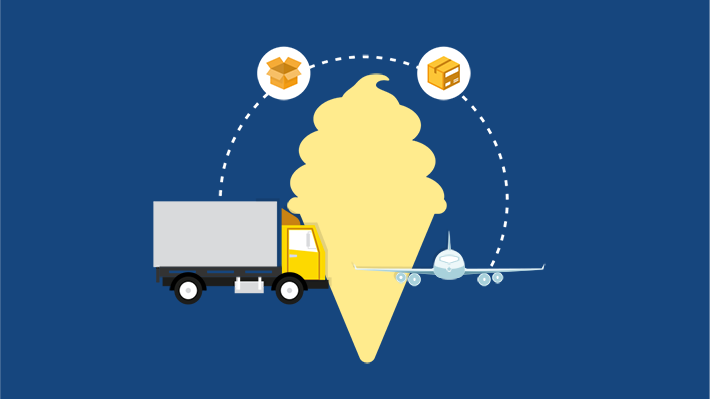
A Conversation with John DiLenge, Director of Global Supply Chain at Rita’s Italian Ice
August 13, 2018
To lead the transformation of supply chains into the next decade, professionals must identify the opportunities and challenges facing their supply chain processes and consider the resulting impact on the organization, its products and services, and its interactions with suppliers, customers and partners. Drexel LeBow interviews supply chain executives to learn about their roles, their current initiatives and practices, and the future direction of their organizations.
Q. What are the key priorities and functions of your role as Director of Global Supply Chain at Rita’s Italian Ice?
Key priorities and functions include procurement for the brand (including proprietary, off-the-shelf items and equipment for the 600 stores), distribution of foods and packaging for all the stores, sales and operations planning, and sourcing of new items.
Q. Compared with other products such as consumer packaged goods, what is special about Rita’s “cold” supply chain? What are the major challenges?
Rita’s signature products are actually manufactured in the stores, so we ship raw materials that are concentrated and have specific temperature requirements. Rita’s also has to ship products in multiple temperatures (frozen, refrigerated, and ambient).
Q. It is essential to maintain good quality in terms of taste, freshness, and food safety. What practices have been adopted for quality control at Rita’s?
All manufactured items go through a strict quality control process – including microbiological testing – before they are released for distribution. All manufacturers we use for the proprietary items must also adhere to safe quality food certification. Stores check temperatures on deliveries at the time of delivery and reject them if they are not within the standards. After products are in stores, each location follows various operational guides to ensure that the finished product aligns with the brand’s specifications.
Rita’s has a team of regional franchise business consultants and uses independent third-party auditors to audit whether franchisees are making products to specifications. Rita’s also has an online quality feedback system to gather information and report on various issues, independently submitted by the field, that are reviewed by supply chain, operations, and research and development teams.
Q. How do franchisees influence supply chain management? For instance, are sourcing, logistics, and quality control centrally controlled?
The supply chain is managed and controlled centrally, but through our distributor network. The franchisees can, and do, influence the managed supply chain through direct communications as well as through the collective voice of the franchise advisory committee. Many of the adjustments made to the collective supply chain come as a result of the franchisee feedback. Surveys are also conducted periodically to gather feedback.
Q. What skills are important for a recent graduate to have a successful career in supply chain management?
- Critical thinking - Don’t just solve the immediate need. Think multiple steps ahead.
- Data analysis - Track what is most important and show how a change can affect the key performance indicators.
- Communications - Use all modes if necessary, but stay consistent, and don’t wait and assume too much. Confirm the assumptions and document them.
> Learn more about Drexel LeBow’s MS in Supply Chain Management and Logistics program.